|
Dear
Subscriber,
Please
support our next Conference on Future
Energy (SPESIF-COFE5) by sending in
your abstract for a paper. The deadline has been
extended to October 15, 2011 if you can also
add a draft of your paper too. We also look
forward to having one or more demonstrations at
the conference as well, so those proposed papers
or proposed presentations will be given special
attention. Exhibit tables are available FREE to
presenters upon request.
We are
excited to see any unconventional energy generator
get to the level of a one megawatt demonstration
plant. That is what is expected of Rossi's E-cats
in the #1 article in October. The video online
gives a walk-through tour of the plant. Of course,
thermal energy still needs to be converted to
electrical, with the usual energy losses, but most
of the conventional utility generation in the
country has that problem. In related news, the low
energy nuclear reaction (LENR) field is heating up
and so a two-day course is being offered on the
developments in LENR on October 3-4, 2011 at the
Hyatt Regency in Crystal City VA by a start-up company called
NUCAT.
Talking
about heat, our #2 story has another approach for
dealing with the wanton wastefulness of industrial
processes by converting it with polymer
pyroelectric materials into electricity.
Two
years after Dr. Glen Gordon's last contribution to
the field of bioelectromagnetics, his EM-Pulse still makes
news with the #3 story that revisits the
importance of a NASA study which he relied upon.
Glen used to emphasize the value of a fast rise
time for any pulsed electromagnetic (PEMF) device
in order to stimulate the HSP70 protein which is a
restorative and regenerative protein that repairs
any number of injuries before inflammation occurs,
so the sooner such a device is used, the better.
Now the NASA study is online for a free download
and IRI still has a few of his EM-Pulse devices
available.
It's
great to see new applications of battery
technology where no man has gone before, like on a
ship (Story #4) and for lightweight applications
with carbon fiber, concrete or plastic. (Story
#5).
Thomas Valone,
PhD, PE Editor
www.IntegrityResearchInstitute.org | |
| |
1)
Rossi's One Megawatt
Plant |
By: Mats Lewan
Publicerad igår, 07:00 Sept. 15, 2011
http://www.nyteknik.se/nyheter/energi_miljo/energi/article3264361.ece
Ny Teknik got a look at the plant
last week in Bologna, where it had been assembled
from parts supposedly manufactured in Rossi's
factory in Miami, Florida.
The plant consists of 52 'E-cats' of a new
model that Rossi says he developed this spring,
partly through discussions with the Swedish
physicists Sven Kullander and Hanno Essen, mainly
regarding research done by Hidetsugu Ikegami, a
professor emeritus at Osaka University in
Japan.
The plant was supposed originally to consist of 100 units of an
early model, rated at a power output of ten
kilowatts. When manufacturing started Rossi stated
that he instead chose a smaller, more stable model
with a power of about three kilowatts, and that
300 such units would then be used.
In July, Rossi changed his mind after
claiming to have reached 27 kilowatts of power
output with the latest model, then discarded the
previously manufactured units.
The 52 units were mounted in four rows along both
sides of a 20-foot container. On the front of each
unit is a valve for filling hydrogen, as well as
electrical connections to the electric resistance
used to 'ignite' the reaction.

Steam outlet hoses are connected to a
single isolated thick tube that runs along both
sides and ends on the outside of the container's
short side. On the outside is a water pump for
water intake.
The plant was initially scheduled to be transported to Greece for
the opening in October, in co-operation with the
Greek company Defkalion Green Technologies.
After Rossi's breach of
contract with Defkalion in August and after
Rossi had established contacts with an American
customer, the container is now instead being
shipped to the United States.
According to Rossi, the launch is
scheduled as planned in October, and will be controlled by a "very
important entity" in the U.S. At the launch a complementary part will be
included to attain a power-output rating of one
megawatt, as the 52 units will be operated at
reduced power levels to ensure stability even at
intervals with self-sustained
operation.
Here it is: the plant that according to inventor
Andrea Rossi will produce one megawatt of thermal
energy via an unknown reaction in his 'energy
catalyzer'. The plant is now being shipped to the
United States.
Ny Teknik assisted at a recent test of the
new model running in self-sustained mode - read our report
here.
Video Demo online: http://www.nyteknik.se/nyheter/energi_miljo/energi/article3264361.ece
READ MORE: Our complete coverage on Rossi's E-cat can be found
here.
RELATED
NEWS
A SHORT COURSE IN
LENR
"Perspectives
on Low Energy Nuclear Reactions" is scheduled for
3 and 4 October of this year at the Hyatt Regency
Hotel in Crystal City very near Washington DC. The
motivation for the course is the significantly
increasing interest in our field. It will
provide an effective way to learn the background,
status and prospects for LENR. Instructors
for the course are Grabowski, Hagelstein, Imam,
Kidwell, McKubre, Melich and Nagel.
The
web site for the course is: http://nucat-energy.com/short-course/.
The
course is sponsored by a new company NUCAT Energy
LLC. The name NUCATderives from the two
physical levels critical to LENR, namely NUClear
and ATomic.
|
2) Polymer
Sandwich for Heat Conversion from
Waste |
21 July 2011 by Ferris
Jabr
http://www.newscientist.com/article/mg21128215.900-polymer-sandwich-harvests-electricity-from-waste-heat.html
IN 314 BC the Greek philosopher
Theophrastus noticed something unusual: when he
heated a black crystalline rock called tourmaline,
it would suddenly attract ash and bits of straw.
He had observed what we now call pyroelectricity -
the ability of certain crystals to produce a
voltage briefly when heated or cooled. Now the
same phenomenon is being used to convert waste
heat into electricity.

Nearly 55 per cent of all the energy
generated in the US in 2009 was lost as waste
heat, according to research by the
Lawrence Livermore National Laboratory in
California. There have been many attempts at using
this waste heat to generate electricity, so far
with only limited success.
Pyroelectricity could be the key, say
Scott Hunter and
colleagues at Oak Ridge National Laboratory in
Tennessee. They have built an energy harvester
that sandwiches a layer of pyroelectric polymer
between two electrodes made from different metals.
Just a few millimetres long, the device is
deployed by wedging it between a hot surface and a
cold surface - between a computer chip and a fan
inside a laptop, for example. Crucially, the
device is anchored to the hot surface alone and so
acts as a cantilever - a beam supported at one
end.
As the device warms, the polymer
expands more than the electrode close to the cold
surface, and the whole device bends like the
bimetallic strip in a thermostat. It droops toward
the cold surface, where it cools and then springs
back toward the hot surface, warming up again.
Soon the cantilever is thrumming between the hot
and cold surfaces like the hammer of a wind-up
alarm clock. Each time it is heated, the polymer
generates a small amount of electricity which is
stored in a capacitor (Proceedings of SPIE,
DOI:
10.1117/12.882125).
Previous attempts at using
pyroelectric materials to recycle waste heat have
only managed to turn 2 per cent of the heat into
electricity. Hunter believes his device could
achieve an efficiency of between 10 and 30 per
cent.
Hunter says the device can also
convert heat in exhaust gases into electricity. It
might even be used to capture the energy that
solar cells lose as heat, he says. Energy
generation aside, he adds that the devices could
soak up enough heat to play a significant role in
cooling laptops and data centres.
Laurent Pilon of
the University of California, Los Angeles, who
also studies pyroelectric energy harvesting, says
he likes the compactness of the device and its
relative simplicity, but has some doubts about the
potential efficiency. "I think some of their
expectations are a little exaggerated," he says.
"They are relying on conduction to heat the
device, which is a slow process." He and other
groups have used fluids to heat or chill a
pyroelectric material. This is much quicker,
though the need to pump the fluid around does
consume some of the energy
generated.
|
3)
Pulsed Electro-Magnetic Fields (PEMF) Four
Year Study by NASA
|
May 22,
2011 // by
drashoksinghal100 // Blog
// 8Comments
Ed. Note: Dr. Glen
Gordon, a former COFE speaker, washighly
influenced to develop the EM-Pulse technology that
IRI still sells, based on the preliminary results
of this NASA study. -
TV
|
Glen Gordon, MD, EM Pulse
PEMF
Device |
NASA 4-year
collaborative study on the efficacy of
electromagnetic fields to stimulate growth and
repair in mammalian tissues has definitive results
according to CHIEF INVESTIGATOR: Thomas J.
Goodwin, Ph.D.Lyndon B Johnson
SpaceCenter.
PURPOSE: This four year
study used human donors "to define the most
effectiveelectromagnetic fields for enhancing
growth and repair in mammalian tissues."
To utilize "nerve
tissue which has been refractory to efforts to
stimulategrowth or enhance its repair regardless
of the energy used." (all othertissues have
demonstrated growth and repair stimulation with
appropriate PEMF)
To define a PEMF
technology that would "duplicate mature, three
dimensionalmorphology between neuronal cells and
feeder (glial) cells, which has not beenpreviously
accomplished."
RESULTS: The PEMF used
in the study "caused accelerated growth rate and
betterorganized morphology over controls", and
resulted in "greater cellviability" (85% vs.
65%).
In the gene discovery
array (chip technology that surveyed 10,000 human
genes),the investigators found up-regulation of
150 genes associated with growth andcell
restoration.
T.Goodwin (personal
communication) " PEMF shut down each dysregulatory
gene we studied".
NASA's CONCLUSION:
"The up-regulation of
these genes is in no manner marginal (1.7-8.4
logs) with genesites for collagen production and
growth the most actively stimulated."
"We have clearly
demonstrated the bioelectric/biochemical
potentiation of nervestimulation and restoration
in humans as a documented reality".
"The most effective
electromagnetic field for repair of trauma was
square wave witha rapid rate of change (dB/dt)
which saw cell growth increased up to
4.0times."
They further noted that
"slowly varying (millisecond pulse, sine wave) or
nonvarying DC (CW lasers, magnets) had little to
no effect."
Final
Recommendation: "One may use square wave
EM fields with rapid rate ofchange for":
1) repairing
traumatized tissues 2) moderating some
neurodegenerative diseases 3) developing
tissues for transplantation
PEMF
PROVIDES:
·GREATER
CELL VIABILITY
·ACCELERATED CELL GROWTH·BETTER
ORGANIZED CELL MORPHOLOGY·UPREGULATION OF
GENESRELATED TO COLLAGEN PRODUCTION
·UP
REGULATION OF GENES RELATED TO CELL RESTORATION
AND GROWTH·BIOELECTRIC POTENTIATIONOF NERVE
STIMULATION AND RESTORATION·HIGH-SPEED SQUARE WAVE
INCREASEDCELL GROWTH FOUR-TIMES
FASTER.
For More
Information:
http://www.integrityresearchinstitute.org/catalog/bioelectric.html
*the first study
to clarify technologies and efficacy parameters
for tissue growthand restoration
|
4)
Zero-Emission Hydrogen Powered Prototype Vessel
|
ScienceDaily (Sep. 2,
2011) - Swiss Federal Laboratories for
Materials Science and Technology (EMPA)
Researchers have been operating a
canal boat with a fuel cell drive for three years
now. In the world of shipbuilding, however,
different rules apply than those in the automobile
manufacturing industries. Weight is of practically
no significance, but the propulsion plant must
have an operating lifetime as long as that of the
boat itself. The hydride storage system -- the
hydrogen tank -- must meet this challenging
requirement.
One
of the most efficient means of transporting
freight is by ship. However, many of the ships
sailing today are powered by aging diesel motors
fitted with neither exhaust cleaning equipment nor
or modern control systems. Three years ago the
University of Birmingham initiated an ambitious
trial, converting an old canal barge to use
hydrogen fuel.
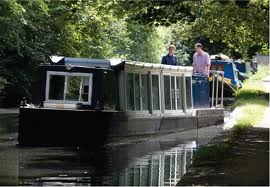 |
The Ross Barlow Zero
Emission Canal
Vessel |
The
old diesel motor, drive system and fuel tank were
removed and replaced with a high efficiency
electric motor, a battery pack for short-term
energy supply and a fuel cell with a hydrogen
storage system to charge the batteries. In
September 2007 the converted boat, the "Ross
Barlow," was launched on its maiden voyage on
Britain's 3500 km long canal system. Last year the
barge made its longest voyage to date, of four
days duration and 105 km length, negotiating no
less than 58 locks. A good opportunity to look
back and take stock.
Mass-produced
drive system meets tailor-made storage
technology
The
first task to be done in converting the 18 m long
steel-hulled barge was to calculate the power
requirements. Based on experience with other
battery driven canal boats it was decided to use a
10 kW permanent magnet motor. To provide energy
for longer trips a commercial fuel cell delivering
1 kW of power was chosen. This system was
originally designed as an uninterruptible power
supply (UPS) for use in the telephone industry.
The capacity of the fuel cell was, however
insufficient to power the boat directly, so the
"Ross Barlow" was also fitted with a 47 kWh buffer
battery. Lead acid batteries were used for this
purpose since they are low maintenance, low-priced
and easy to charge. The weight of the battery pack
is of no consequence when used in an inland
waterways vessel.
The
hydrogen supply for the fuel cell was provided by
hydride storage system developed by Empa and
partly financed by the Swiss Federal Office of
Energy (SFOE). This device can store hydrogen with
an energy content of 50 kWh, which is equivalent
to 20 pressurized gas cylinders each of 10 Liter
capacity. The storage material consists of an
alloy of titanium, zirconium, manganese, vanadium
and iron in powder form which is packed into
sealed steel tubes. The powder absorbs hydrogen,
thus acting as a storage medium, only releasing it
when heated. Since when "filling up" with hydrogen
the metal powder generates heat which must be
removed, each storage module is located in a water
tank which can be warmed or cooled as necessary,
In addition the ship is fitted with a solar panel
which can supply up to 320 W of electric
power.
 |
The hydride storage system
developed by Empa was partly financed by the
Swiss Federal Office of Energy
(SFOE). |
Charging
and discharging cycles -- for the next 100
years!
The
journey through canals and locks makes widely
varying demands on the barge's electrical supply.
To save wear and tear on the fuel cell, the motor
draws its current from the lead acid batteries
during routine sailing. A typical journey takes 4
to 6 hours during which time the canal boat uses
12 to 18 kWh of power. In continuous operation the
fuel cell delivers 24 kWh of energy per day. This
also powers the electronic monitoring system,
leaving about 19 kWh with which to charge the
buffer battery pack -- enough energy for a daily
journey lasting six hours.
The
reliability and operational lifetime of the metal
hydride storage system was tested in the
laboratory during its development. In practical
terms this means that when used to power the "Ross
Barlow," if the ship is assumed to travel 650 km
per year through the British canal system, it
would need refueling once a month with hydrogen.
In this case the hydrogen storage system would
have an operating lifetime in excess of 100 years,
and would therefore comfortably outlast the useful
lifetime of the barge itself.
The
results of the test voyage
During
the 105 km, four-day summer test journey a total
of 106 kWh of electric energy was consumed on the
"Ross Barlow," including lighting and recharging
the crew's mobile telephones and laptop
computers.
The
batteries supplied 71 per cent of this energy, the
hydrogen fuel cell 25 per cent and the solar panel
4 per cent. There was unanimous praise from the
crew for the practically silent way the boat
sailed. Also notable was that when waiting in a
lock the "Ross Barlow" was not engulfed by its own
diesel fumes. The boat which accompanied it (which
was about the same size) used some 50 L of diesel,
resulting in a CO2 emission of approximately 133
kg. The "Ross Barlow" on the other hand produced
no CO2 during its voyage, assuming that the
hydrogen it used was derived from renewable
sources and delivered free of emissions to the
refueling point on the bank of the canal.
back to table of
contents
|
5)
Recharging the Battery: Hidden
Power |
by James Mitchell Crow Aug.
25,2011, New Scientist issue 2827. http://www.newscientist.com/article/mg21128272.300-recharging-the-battery.html?full=true
IF THERE is one thing that symbolises the
incredible success - and dismal failure - of
21st-century technology, it is the battery. Each
year we spend some $50 billion on the things,
mostly to go in our cameras, cellphones and
laptops. They give us abilities our parents could
only dream of. Yet batteries are also a titanic
headache, both for engineers who must squeeze
these objects into tight spaces, and for the
millions of us who curse them whenever our gadgets
run out of juice.
Help could finally be at hand, though, now
that researchers are starting to rethink
electrical storage from the bottom up. They
foresee a time when the very fabric of modern life
- ordinary materials such as plastics and concrete
- will hold much of the electricity we need.
Utilising familiar stuff in this way not only
promises to keep the power flowing wherever we go,
but it could signal the end of the battery as we
know it. In future, that plastic casing on your
smartphone won't just protect the circuits inside;
it will keep them supplied with juice too. The
walls and floors of your home could also do double
duty - as infrastructure that also keeps the
lights burning. Even humble paper could play a
vital role in keeping you switched on.
According to Emile Greenhalgh, one
of the first places you'll notice a difference
will be on your driveway. Though your next car is
likely to look familiar, its sleek bodywork could
well be made from lightweight composites rather
than steel. And if Greenhalgh, a materials
scientist at Imperial College London, has his way,
this bodywork will help store the energy that your
vehicle's electric motor needs for the daily
commute. "We think the car of the future could be
drawing power from its roof, its bonnet or its
door," he says.
His vision emerged in 2003, when he was
approached by researchers from the UK government's
research agency, the Defence Science and
Technology Laboratory. They were after a new
material for uncrewed aerial vehicles that would
be strong enough to bear a load but could also
store electrical energy. Greenhalgh and his
colleagues were intrigued and set out to design
one.
They began with a material that is already
revolutionising the aerospace industry: carbon
fibre. The stuff is renowned for high strength and
low weight. When used to reinforce plastic resins,
it forms a tough composite used in Formula One
racing cars and new passenger jets like Boeing's 787
Dreamliner. Though carbon-fibre composites are
not known for electricity storage, the fibres are
good electrical conductors - useful when you want
them to store charge. "Some commercially available
carbon fibres perform really well as electrodes,"
says Leif Asp of the Swerea Sicomp research
institute in Gothenburg, Sweden. "That was not
what we expected."
Rather than building a battery, Greenhalgh
decided to focus efforts on developing another
energy-storage device: a capacitor, or in this
case a souped-up "supercapacitor". A battery has
two electrodes separated by an electrolyte. The
difference in electric charge between the
electrodes causes charged ions to flow through the
electrolyte when the battery is part of a circuit,
causing current to flow. Batteries therefore store
electricity in chemical form, while in capacitors
all the charge accumulates on the electrodes, and
an insulating layer keeps these charges apart. The
solidity of a capacitor is what makes them easier
to adapt for load bearing.
The key to creating a capacitor that can
store electricity in amounts useful to your
gadgets is to maximise the electrodes' surface
area. So Greenhalgh coated each carbon fibre with
a bristling layer of conducting carbon-nanotubes.
He then weaved this furry spaghetti into two flat
electrodes, added an insulating fibreglass layer
between them, and encased the lot in a polymer
resin.
The nanotubes brought an unexpected
benefit - they not only stored a lot of charge,
but they made the supercapacitor panel extremely
strong. In part, this is down to their surface
area, which helps to create a better bond between
the fibres and the resin. The nanotubes also act
like guy ropes, extending out from the slender
carbon fibres and helping to stop them from
buckling under a load. The result is a tough,
lightweight panel that can store 1 watt-hour per
kilogram, around 1/20th of the capacity of a
conventional supercapacitor (see
chart).
Greenhalgh now heads a European-wide
project called Storage, which, in partnership with
Volvo, aims to construct a hybrid-electric car in
which a large steel panel in the vehicle's floor
will be replaced by a composite
supercapacitor. By shrinking the main battery
and eliminating heavy steel, the panel should
shave some 15 per cent from the vehicle's weight.
However, though Greenhalgh is confident he can
improve on his supercapacitor's existing storage
capacity, he admits that you will probably never
drive an electric vehicle powered solely by such
capacitors as they are unlikely to ever match the
capacity of lithium-ion batteries.
Lightweight laptops
Still, such panels offer significant
advantages, particularly for hybrid cars with
regenerative braking, which slows a car by
converting the kinetic energy of movement into
electrical energy. Supercapacitors are perfectly
suited for collecting these short bursts of energy
and putting it back into the system when they
accelerate. That means the main battery can be
smaller and lighter, and should last longer in
service.
That said, other members of the Storage
consortium are still keen to entirely eliminate
conventional hybrid-vehicle batteries. Asp, in
particular, wants to turn lithium-ion batteries
themselves into structural composites. Again,
carbon fibre is a surprisingly good place to start
as one of the electrodes in a conventional
lithium-ion battery is usually made from graphite,
and carbon fibres are essentially graphite
threads.
Batteries are tricky to adapt to a dual
role, though, because their electrolyte is often a
gel or liquid. So Asp's team is formulating a mix
that incorporates a tough polycarbonate as well as
a liquid electrolyte. Asp claims its capacity will
eventually match that of existing lithium-ion
batteries.
Asp's "composite battery" could eventually
offer lightweight versions of conventional laptops
and cellphones, or new designs that run for longer
without needing a recharge. However, that might
not happen overnight, as carbon-fibre composites
aren't cheap. When they are eventually
commercialised, structural batteries are likely to
appear only in the most expensive products at
first. That might not include cars, though. "What
Volvo has found with electric cars is that steel
is too heavy. They have to go to composite cars
anyway," says Greenhalgh. "Our material gives a
bonus."
Structural batteries need not always be
expensive, though; they can also be based on
seriously low-tech materials - stuff so cheap that
you wouldn't think twice about parking your car
right on top of it. In 2007, two researchers at
the University of Cambridge laid the foundations
for a future in which concrete walls, floors and
even driveways could double up as huge batteries.
Gordon Burstein and Erek Speckert reckoned that,
because concrete contains millions of tiny
water-filled pores, it should behave like an ionic
conductor. When sandwiched between a steel cathode
and an aluminium anode, their prototype battery
did produce a trickle of current - until the
electrodes succumbed to corrosion (ECS
Transactions, DOI:
10.1149/1.2838188).
This unpromising start has inspired fresh
attempts, however, including a concrete
zinc-carbon battery created by a team at the State
University of New York at Buffalo. The anode of
their three-layered concrete composite contains
carbon black and zinc powder while the cathode
contains carbon black and manganese dioxide powder
(see diagram). The idea is that these finely
dispersed materials improve electrical
connectivity between the electrodes and the
electrolyte, and this works, up to a point. Tests
show their battery's storage capacity is still
minuscule - just microwatt-hours per kilogram -
but the researchers say that adding salts or
polymers to tune electronic and ionic conductivity
should improve its performance (Cement and Concrete
Composites, vol 32, p 829).
Considering that the average American
house contains over 12 tonnes of concrete and a
small office block might use a thousand times
more, concrete batteries would seem to offer huge
capacity for electrical storage, particularly in
off-grid buildings, as emergency back-up supplies
for businesses or for smoothing the output from
roof-mounted photovoltaic panels. For now, though,
you are more likely to be plugging in to your
wallpaper than to the wall behind it.
Paper-thin batteries are already highly
desirable for powering circuitry in everything
from electronic newspapers to the ultimate geek
chic: clothing with gadgets like phones and
music-players built in. Shreefal Mehta thinks that
paper itself holds the key.
Mehta runs the Paper Battery Company based
in Troy, New York, and is working towards
electricity-storing sheets that will not only
squeeze into places that conventional batteries
can't reach - thin gaps in cellphone casings, say
- but which could also replace paper and thin
plastic in almost any situation where electricity
storage would be a bonus.
Electric origami
His battery is based on research by a team
at Rensselaer Polytechnic Institute (RPI), also in
Troy, that showed it is possible to store energy
in a sheet of cellulose. The team embedded a
carbon-nanotube array into each side of a
cellulose sheet that had been soaked in an ionic
liquid. The nanotubes formed the electrodes, while
the ionic liquid, dispersed in pores within the
cellulose, acted as an electrolyte. Their material
successfully stored around 10 watt-hours per
kilogram - in other words, a dozen A4 sheets of
the stuff would supply about the same energy as a
typical AAA-battery (Proceedings of the
National Academy of Sciences, vol 104,
p 13574).
Though Mehta declined to reveal much about
the material his company is developing, dubbed the
PowerWrapper, he says their trick has been to
formulate the different components into a
printable ink so that they can create a battery by
printing the layers sequentially. This allows them
to create both supercapacitors and batteries with
high energy-density that can be produced using a
high-speed roll-to-roll manufacturing process.
Mehta plans to commercialise his paper batteries
in the next two years. "We're already in
discussions with customers who are testing our
prototype devices," he says.
Ultimately, the company envisages
integrating their paper battery into the cover or
lining of laptop cases, into car interiors and
homes. A PowerWrapper sheet could do the job of a
conventional membrane laid under the roof or fixed
to exterior or interior walls, while also allowing
you to store renewable energy from photovoltaic
panels or turbines for times when the sun isn't
shining or the wind doesn't blow. "You could wrap
it around any structure," says Pulickel Ajayan,
who helped develop the material at RPI.
So tread lightly on that concrete path.
Close your laptop's lid with care. We may not wave
goodbye to AA-batteries and their ilk for some
while yet, but in the meantime let's show the
everyday materials of modern life the respect they
will soon deserve.
James Mitchell
Crow is a science writer based in
Melbourne, Australia
back to table of
contents |
About Integrity
Research Institute
Future
Energy eNews is
provided as a public service from Integrity Research
Institute, a
Non-Profit dedicated to educating the public
on eco-friendly emerging energy technologies.
FREE copy
of the 30 minute DVD "Progress in Future Energy"
is available by sending an email with "Free DVD" in subject
and mailing address in
body.
Your
generous support is welcome by making a tax
deductible donation on our
secure website | | | |
Save 10% |
On
all purchases from IRI by becoming a
member and
a free gift when you join and you save 10% on all
conference and workshop fees as well. You
will receive a quarterly mailing with the latest
information on eco-friendly emerging energy
technologies. All 2011 IRI members will receive free
copies of Energy magazines and the latest emerging
energy technologies reports. |
| | | |